Case Study
Home ยป Quality Control in Pharmaceuticals
Quality Control in Pharmaceuticals
Problem Statement
A pharmaceutical manufacturer faced significant challenges in ensuring consistent quality during the production of medications. Manual quality control processes were prone to errors and inefficiencies, leading to product recalls and compliance risks. The company needed an advanced solution to automate quality control, reduce production errors, and comply with stringent regulatory standards.
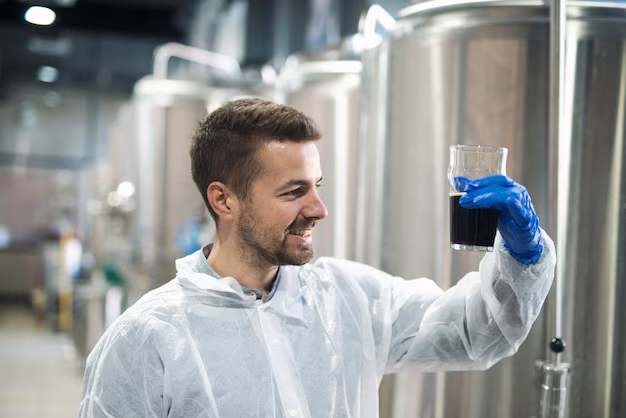
Challenge
Implementing automated quality control in pharmaceutical manufacturing posed several challenges:
- Detecting microscopic defects, contamination, or irregularities in products and packaging.
- Ensuring high-speed inspection without disrupting production workflows.
Meeting strict industry regulations for product quality and traceability.
Solution Provided
An AI-powered quality control system was developed using machine vision and advanced inspection algorithms. The solution was designed to:
- Automatically inspect pharmaceutical products for defects, contamination, and compliance with production standards.
- Analyze packaging integrity to detect labeling errors, seal defects, or missing components.
- Provide real-time quality control insights to production teams for immediate corrective actions.
Development Steps

Data Collection
Captured high-resolution images and videos of pharmaceutical products during production, including tablets, capsules, and packaging components.

Preprocessing
Preprocessed visual data to enhance features such as shape, texture, and color, enabling accurate defect detection.

Model Training
Developed machine vision models to detect defects and anomalies at microscopic levels. Integrated AI algorithms to classify defects and provide actionable insights for process improvement.

Validation
Tested the system on a variety of production scenarios to ensure high accuracy and reliability in defect detection.

Deployment
Installed AI-powered inspection systems on production lines, integrating them with existing manufacturing processes and quality control frameworks.

Continuous Monitoring & Improvement
Established a feedback loop to refine models based on new production data and evolving quality standards.
Results

Increased Quality Assurance Accuracy
The system achieved a significant improvement in defect detection accuracy, ensuring product quality.

Reduced Production Errors
Automated inspection minimized human error, resulting in fewer production defects and higher consistency.

Ensured Regulatory Compliance
The solution enabled the manufacturer to meet industry regulations and maintain traceability of production data.

Enhanced Operational Efficiency
Real-time defect identification reduced downtime and improved production throughput.

Cost Savings
By preventing defects and recalls, the company saved on rework costs and protected its reputation.