Case Study
Home » AI for Predictive Maintenance in Renewable Energy
AI for Predictive Maintenance in Renewable Energy
Problem Statement
Renewable energy providers face significant pressure to maximize uptime and minimize maintenance costs for wind turbines and solar panels, amidst fluctuating environmental conditions and rising energy demands. Our client, a global renewable energy company, sought to utilize AI modeling to predict equipment failures proactively, reduce downtime, and enhance energy output, ultimately improving operational reliability and cost efficiency.
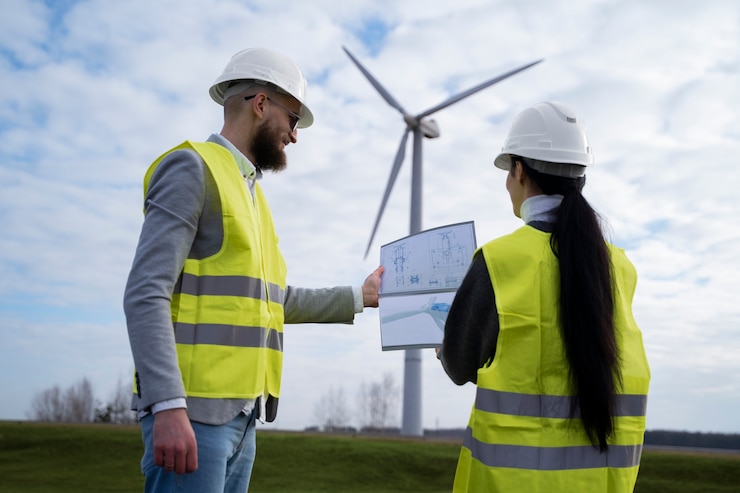
Challenge
The primary challenges in deploying AI for predictive maintenance included:
- Data Complexity: Processing diverse, high-volume data from IoT sensors, weather patterns, and equipment logs, often in real time.
- Prediction Accuracy: Developing a model capable of accurately forecasting failures to enable timely interventions without false positives.
System Integration: Seamlessly embedding the AI solution into existing operational systems for real-time monitoring and actionable insights.
Solution Provided
The solution harnessed machine learning and IoT integration to create a predictive maintenance system for wind turbines and solar panels. The system was designed to:
- Analyze Performance Data: Use time-series analysis to detect anomalies and predict potential failures based on equipment and environmental data.
- Enable Proactive Maintenance: Provide real-time alerts to technicians, prioritizing maintenance tasks to prevent downtime.
- Optimize Energy Output: Identify inefficiencies in equipment performance to maximize energy generation and system longevity.
Development Steps

Data Collection
Aggregated historical and real-time data from IoT sensors, maintenance logs, and weather forecasts to build a comprehensive dataset.

Preprocessing
Cleaned and standardized data, addressing missing values, normalizing sensor inputs, and aligning time-series records.

Model Development
Trained machine learning models using time-series analysis and algorithms like LSTM (Long Short-Term Memory) to predict equipment failures.

Validation
Evaluated model performance with metrics like precision, recall, and mean time to failure, refining predictions through cross-validation.

Deployment
Integrated the AI system into the client’s operational dashboard, enabling real-time monitoring and automated alerts.

Continuous Monitoring & Improvement
Monitored model accuracy and updated it with new data to adapt to evolving equipment conditions and environmental factors.
Results

35% Less Downtime
Proactive failure predictions reduced unplanned outages, ensuring consistent energy production.

20% Lower Maintenance Costs
Targeted repairs minimized unnecessary servicing, extending equipment lifespan.

10% More Energy Output
Optimized performance increased overall energy generation efficiency.

Improved Operational Efficiency
Real-time alerts streamlined maintenance scheduling, reducing operational disruptions by 25%.

Enhanced System Reliability
Data-driven insights strengthened the resilience of renewable energy systems, boosting client confidence.