Case Study
Home » Automated Manufacturing Defect Detection
Automated Manufacturing Defect Detection
Problem Statement
A manufacturing company struggled with detecting defects in real-time during production. Traditional manual inspection methods were slow, inconsistent, and prone to human error, resulting in increased waste, delayed shipments, and reduced product quality. The company needed an automated solution to improve defect detection accuracy and efficiency while minimizing production waste.
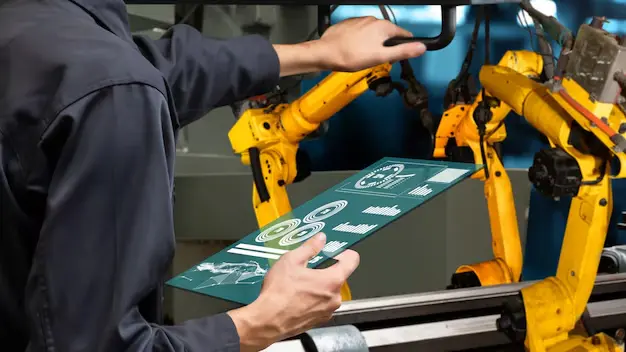
Challenge
Implementing an automated defect detection system involved addressing several challenges:
- Processing large volumes of data from high-speed production lines in real time.
- Accurately identifying subtle defects in products with varying shapes, sizes, and materials.
Integrating the system seamlessly into existing production workflows without disrupting operations.
Solution Provided
An AI-powered defect detection system was developed using computer vision technology and machine learning classification models. The solution was designed to:
- Capture and analyze high-resolution images of products on the production line using computer vision systems.
- Detect and classify defects with high accuracy, including surface scratches, dents, and dimensional inconsistencies.
- Automate defect flagging and reporting to reduce manual intervention and expedite quality control processes.
Development Steps

Data Collection
Captured thousands of product images during production, including both defective and non-defective samples, to build a comprehensive dataset.

Preprocessing
Enhanced image quality, normalized lighting conditions, and annotated defects to prepare data for machine learning training.

Model Development
Developed machine learning models to classify images as defective or non-defective. Trained models using convolutional neural networks (CNNs) for accurate feature extraction and defect recognition.

Validation
Tested the system with real-world production data to ensure high accuracy and reliability in defect detection.

Deployment
Integrated the defect detection system with the company’s production line and quality control workflows, enabling real-time inspection and reporting.

Continuous Monitoring & Improvement
Implemented a feedback loop to refine the model using new data and evolving defect patterns, ensuring continuous improvement.
Results

Increased Defect Detection Accuracy
The system achieved a significant improvement in defect detection accuracy, reducing the likelihood of faulty products reaching customers.

Reduced Waste
Automated identification of defects early in the production process minimized waste by preventing defective products from advancing further.

Improved Product Quality
The solution ensured consistent quality standards, enhancing the company’s reputation and customer satisfaction.

Enhanced Operational Efficiency
Real-time defect detection reduced inspection time and manual effort, streamlining production workflows.

Scalable and Adaptable Solution
The system adapted seamlessly to new product lines and defect types, supporting the company’s evolving manufacturing needs.