Case Study
Home » Edge AI and Real-Time Modeling
Edge AI and Real-Time Modeling
Problem Statement
The manufacturing industry faces significant downtime and maintenance costs due to unexpected equipment failures, impacting productivity and profitability. A leading industrial manufacturer aimed to implement Edge AI and real-time modeling to enable predictive maintenance on factory equipment, minimizing disruptions, optimizing maintenance schedules, and enhancing operational efficiency.
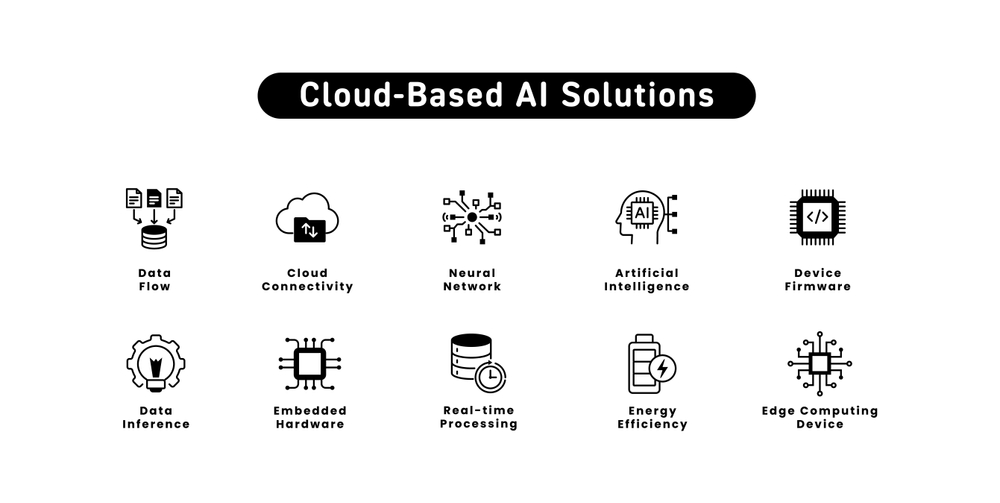
Challenge
The primary challenges in deploying Edge AI for this purpose included:
- Data Processing: Collecting and analyzing high-frequency sensor data from machinery in real time, without relying solely on cloud connectivity.
- Low-Latency Requirements: Ensuring rapid decision-making on edge devices to detect and respond to equipment anomalies instantly.
- Resource Constraints: Developing lightweight AI models capable of running on resource-limited edge hardware without sacrificing accuracy.
Solution Provided
The solution leveraged Edge AI and real-time modeling to monitor equipment health and predict failures proactively. The system was designed to:
- Monitor Equipment: Use IoT sensors on machinery to collect real-time data on vibration, temperature, and pressure, processed locally on edge devices.
- Predict Failures: Deploy compact AI models to analyze sensor data and forecast potential breakdowns, enabling timely maintenance interventions.
Optimize Operations: Provide actionable insights to factory managers and technicians, reducing downtime and extending equipment lifespan.
Development Steps

Data Collection
Installed IoT sensors across critical machinery to gather continuous data on operational parameters.

Preprocessing
Filtered and preprocessed sensor data on edge devices to remove noise and prepare it for real-time analysis.

Model Development
Trained a lightweight machine learning model (e.g., a decision tree or neural network optimized for edge) using historical failure data, then compressed it for deployment on edge hardware.

Validation
Tested the model’s performance on edge devices using metrics like precision and recall for failure prediction, ensuring reliability under real-world conditions.

Deployment
Embedded the AI model into edge devices connected to factory equipment, enabling autonomous, real-time monitoring and alerts.

Continuous Monitoring & Improvement
Periodically updated the edge models with new data via over-the-air updates, adapting to evolving equipment behavior.
Results

Reduced Downtime
Real-time failure predictions decreased unplanned equipment downtime by 30%, boosting production continuity.

Cost Savings
Predictive maintenance cut repair and replacement costs by 20%, optimizing resource allocation.

Improved Efficiency
Edge AI enabled a 25% reduction in maintenance scheduling delays, streamlining factory operations.

Enhanced Safety
Early detection of anomalies reduced workplace incidents by 15%, improving employee safety.

Scalable Deployment
The Edge AI solution was successfully rolled out across multiple factories, demonstrating its adaptability and scalability.