Case Study
Home ยป Smart Manufacturing with Digital Twins
Smart Manufacturing with Digital Twins
Problem Statement
A leading manufacturing company faced challenges in optimizing its operations and minimizing downtime. Traditional methods of monitoring and improving processes were reactive, leading to inefficiencies and increased costs. The company sought a solution to simulate and optimize manufacturing workflows, enabling proactive maintenance and real-time process improvements.
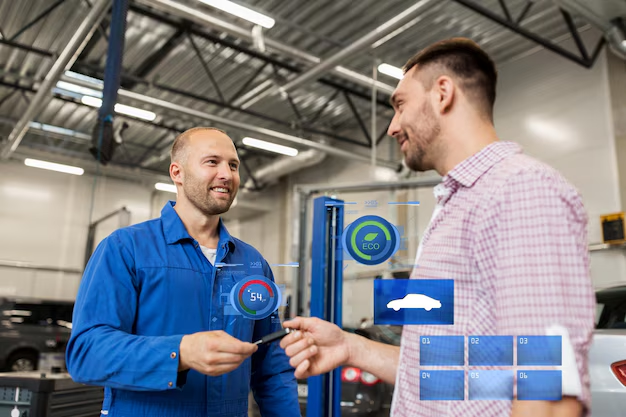
Challenge
Implementing smart manufacturing with digital twins presented several challenges:
- Integrating IoT sensors across complex machinery and processes to collect real-time data.
- Creating accurate digital replicas of physical manufacturing operations for simulation and analysis.
Analyzing large volumes of data to identify inefficiencies and predict potential failures.
Solution Provided
A comprehensive digital twin system was developed using IoT sensors, AI analytics, and digital twin technology. The solution was designed to:
- Create digital replicas of physical manufacturing processes to simulate operations and test optimizations.
- Monitor real-time data from IoT sensors to detect anomalies and inefficiencies.
- Enable predictive maintenance by analyzing equipment performance and predicting failures before they occur.
Development Steps

Data Collection
Deployed IoT sensors across manufacturing equipment to collect data on machine performance, environmental conditions, and workflow metrics.

Preprocessing
Standardized and cleaned data to ensure accuracy and compatibility for simulation and analytics.

Digital Twin Development
Created digital replicas of manufacturing processes, integrating real-time data streams for continuous updates. Built simulation models to test workflow optimizations and predict the outcomes of process changes.

Validation
Tested the system in simulated environments to ensure accuracy in predicting outcomes and optimizing processes.

Deployment
Implemented the digital twin system across manufacturing facilities, integrating it with existing management tools for seamless operation.

Continuous Monitoring & Improvement
Established a feedback loop to refine simulations and analytics based on new data and operational changes.
Results

Improved Operational Efficiency
The system optimized workflows, reducing bottlenecks and improving overall efficiency in manufacturing processes.

Enabled Proactive Maintenance
Predictive maintenance minimized downtime by identifying potential equipment failures before they occurred.

Optimized Resource Usage
Simulations allowed the company to test process changes virtually, reducing waste and optimizing resource allocation.

Enhanced Decision-Making
Real-time insights and simulations enabled data-driven decisions, accelerating innovation and process improvements.

Scalable and Future-Ready
The digital twin system scaled effortlessly across facilities and adapted to new manufacturing technologies, ensuring long-term viability.